Acompanhe os passos da análise completa do sistema de injeção common rail da Bosch no motor FPT F1C, que equipa caminhões Iveco Daily 70C16
Texto: Fernando Lalli
Fotos: Fernando Lalli
Quando se trata de injeção diesel, o common rail domina o mercado. Presente na maioria dos caminhões e ônibus que rodam atualmente nas ruas e estradas brasileiras, este sistema de injeção ajudou a revolucionar o mercado diesel no Brasil nos últimos 15 anos. Entretanto, é um sistema complexo. Sua reparação necessita que a Acompanhe os passos da análise completa do sistema de injeção common rail da Bosch no motor FPT F1C, que equipa caminhões Iveco Daily 70C16 Fernando Lalli Fernando Lalli oficina tenha os equipamentos corretos para garantir, além de precisão, a velocidade que o cliente precisa. Um diagnóstico muito longo gera prejuízo tanto para o dono do veículo quanto para o dono da oficina. “Quando falamos em reparação de common rail, os diferenciais que o mecânico deve ter são capacitação, equipamentos e agilidade”, declara o instrutor de sistemas diesel da Bosch, Rafael Amorim. “O profissional que faz esse diagnóstico rápido, resolve rápido o problema e ganha dinheiro mais facilmente, então, ele precisa saber quais ferramentas utilizar e como utilizá-las”.
No exemplo desta reportagem, foi utilizado o motor F1C, fabricado pela FPT, que equipa caminhões Iveco Daily 70C16 ano 2008. Rafael Amorim simulou falhas nas linhas de baixa e alta pressão para exemplificar casos comuns nas oficinas e quais processos devem ser seguidos, sempre dentro da sequência sugerida pelo equipamento de análise.
Procedimento
1. Ao contrário do que muita gente pensa, o primeiro passo a ser executado quando se fala em diagnóstico de sistema common rail é a análise da bateria. A bateria tem uma grande importância, não só para dar partida, mas também para alimentar todos os sistemas eletrônicos embarcados no veículo, tais como chave codificada, central de injeção e outros componentes que tenham influência sobre o funcionamento do veículo. No momento da partida, é importante garantir que a tensão da bateria fi que sempre acima de 9,8 V.
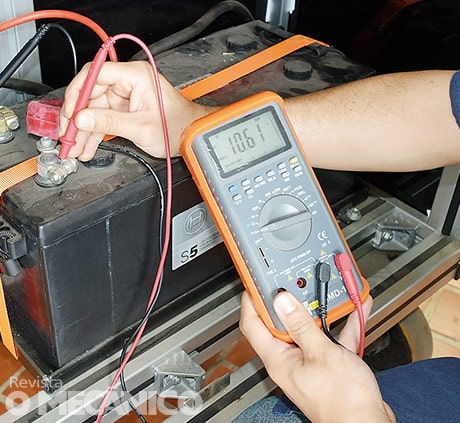
2. O próximo teste a ser feito é medir a pressão do sistema de combustível. Para esse teste, nesta reportagem utilizamos o equipamento Bosch KTS 570, ligado ao sistema de gerenciamento eletrônico do motor. No monitor do aparelho, são mostradas as pressões nominal e efetiva do sistema de combustível. A pressão nominal indicada no aparelho para o motor desta reportagem é 25,7 MPa (sigla para megapascal – 1 megapascal é equivalente a 10 bar). Ao dar partida no veículo, se a pressão efetiva não atingir o valor nominal, será necessário verificar a linha de baixa pressão do combustível.
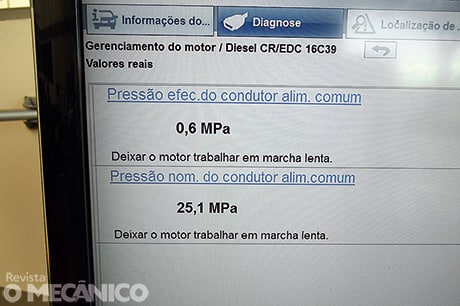
OBS: O sistema common rail é dividido em linhas de baixa pressão, alta pressão e linha de retorno. Cada veículo tem uma pressão de trabalho diferente: isso depende de condições do veículo e do sistema utilizado. Por isso, a consulta ao manual é necessária, uma vez que, se você trabalhar com valores errados você vai ter um diagnóstico errado.
3. Ao diagnosticar a linha de baixa pressão de combustível, o objetivo é atestar que o diesel está saindo do tanque e chegando até a bomba de alta pressão na quantidade e pressão corretas. Para tal, é necessário instalar no sistema um manômetro de baixa pressão após a bomba elétrica de combustível.

4. A pressão de trabalho do circuito de baixa pressão no motor F1C deve ficar entre 4,2 e 4,7 bar. No teste, ao dar a partida no motor, a pressão ficou em aproximadamente 1,5 bar. Portanto, há uma falha no circuito de baixa pressão que deve ser corrigida antes de dar sequência ao diagnóstico.
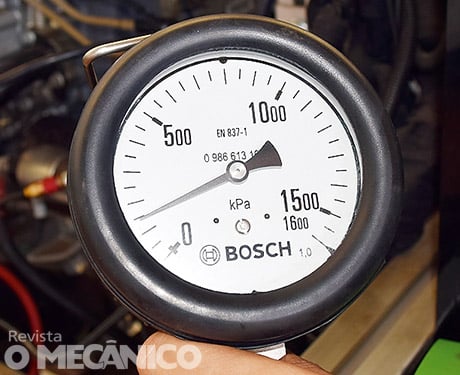
5. O aparelho de diagnóstico KTS 570, utilizado nesta reportagem, mostra ao mecânico a sequência de testes prevista pelo manual de reparo daquele veículo (5a). Cumpridos os passos, constatou-se que o problema na linha de baixa pressão estava na bomba elétrica de combustível. Ao dar novamente a partida, a pressão estava normalizada em aproximadamente 4,5 bar (5b).
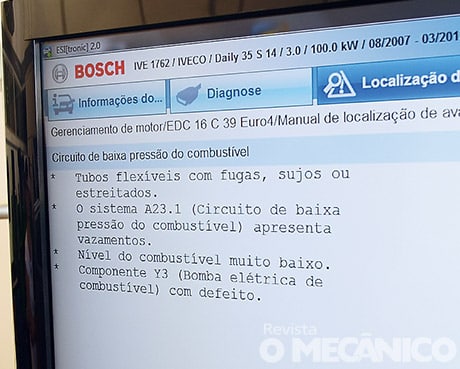

6. Se o motor insistir em não pegar, siga para a análise da linha de alta pressão. Os principais componentes da linha de alta pressão são os injetores, a bomba de alta pressão e o rail (ou flauta).
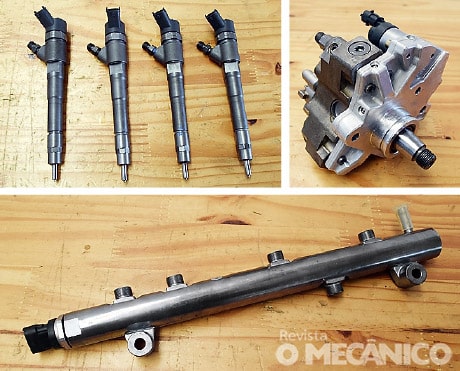
7. O início do diagnóstico do circuito de alta pressão começa pelo teste de resistência da bobina dos injetores. A medição da resistência deve ser feita com multímetro na função ohm (Ω), com as duas pontas de prova nos dois pinos da bobina. Para os injetores do motor F1C, os valores de resistência encontrados devem estar entre 0,5 e 0,7 Ω.
Importante: não utilize a chamada função “bip” do multímetro neste teste. Não basta apenas comprovar que há continuidade na bobina, mas, sim, observar se os valores de resistência estão corretos.
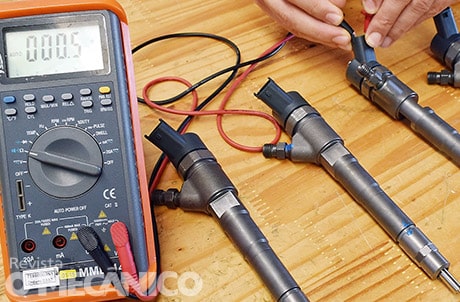
8. A seguir, faça o teste de isolamento dos injetores. Esse teste consiste em medir a resistência entre a bobina do injetor e sua carcaça. Coloque uma das pontas de prova do multímetro na carcaça e a outra em um dos pinos da bobina. Realize a medição nos dois pinos. Em ambos, o valor de resistência encontrado deve ser o mesmo com as pontas do multímetro em circuito aberto, ou seja, resistência infinita. Qualquer valor de resistência que não seja o infinito significa que a bobina do injetor está com problema. O componente deve ser substituído por completo ou encaminhado à autorizada Bosch para os devidos reparos com equipamentos específicos.
Importante: também não utilize a chamada função “bip” do multímetro neste teste. Não basta apenas comprovar que há isolamento na bobina, mas, sim, observar se o valor está correto.
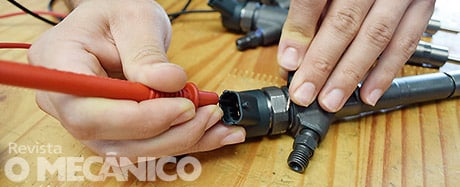
9. Com os injetores ainda instalados no motor, outro teste importante é a medição do volume retorno de combustível. Segundo Rafael Amorim, um injetor danificado apresenta um volume muito alto de retorno. Isso significa uma perda do combustível que estaria no rail ou um desgaste mecânico, o que pode causar falhas no funcionamento do motor.

10. Para instalar a ferramenta medidora de retorno (vendida no mercado pela Bosch), é preciso retirar o conjunto de retorno original: remova os grampos (10a) que fazem a fixação da tubulação em cada injetor, depois solte as conexões (10b). Encaixe as mangueiras de retorno da ferramenta (10c); posicione a ferramenta e dê partida no motor. O combustível começará a subir pelas mangueiras: cada tubo graduado corresponde a um injetor.
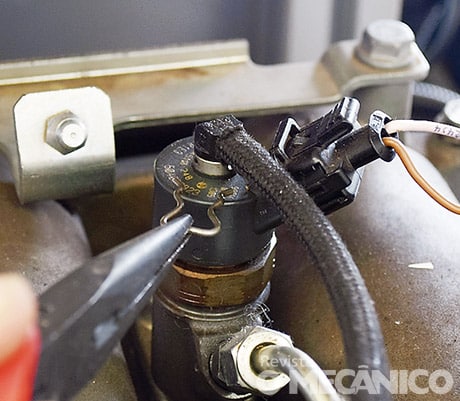

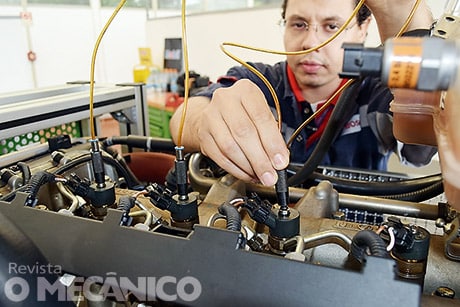
11. Para esta reportagem, Rafael simulou dois problemas. No 1º cilindro, da esquerda para a direita, há o exemplo de um injetor com excesso de retorno. Esse excesso causa falta de pressão de combustível no rail (flauta). Nos outros três cilindros, a variação (dispersão) entre o volume de retorno também pode ser indício de desgaste dos injetores.
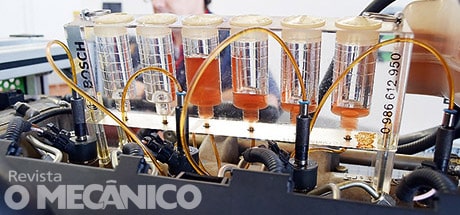
12. Com o uso do scanner KTS, ainda é possível fazer outros testes para avaliar a dispersão ou irregularidades entre o funcionamento dos injetores. Dependendo do veículo, é possível testar o motor durante a partida (teste de compressão) ou também durante a condição de funcionamento em marcha lenta. Com o teste em marcha lenta, é possível saber quanto cada cilindro contribui para essa condição de funcionamento. Já o teste de compressão atua com o motor de partida ligado por cinco segundos, sem colocar o propulsor em funcionamento. Esse teste também avalia o quanto cada injetor contribui para o funcionamento do motor. Em qualquer um dos dois testes, caso a dispersão entre um cilindro e outro seja muito grande, significa que existem falhas no motor, ou no cilindro ou no injetor common rail.

OBS: Após os testes, se for constatado que há indícios de problemas nos injetores, Rafael orienta o mecânico a removê-los e enviá-los a oficinas autorizadas Bosch para realização de testes em bancadas específicas.
Remoção e bancada
13. Para remover o injetor, com o conjunto de retorno já retirado, solte o conector da bobina.
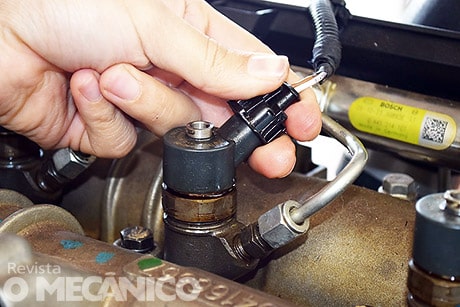
14. Em seguida, desrosquei as duas extremidades dos tubos de combustível com chave 14 mm: primeiro solte o lado do injetor, depois o lado da flauta. Importante: Os tubos de combustível jamais devem ser soltos com o motor em funcionamento, devido às altíssimas pressões de trabalho as quais estão submetidos.

15. Por fi m, solte o parafuso do cavalete de fixação do injetor (15a) e remova o componente (15b). O torque deste parafuso na montagem é de 28 Nm. Segundo Rafael, um torque acima do especificado altera a posição do injetor e influencia em seu funcionamento (15c).
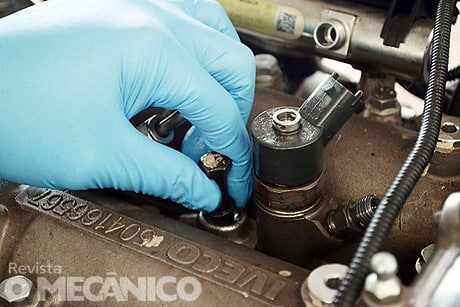
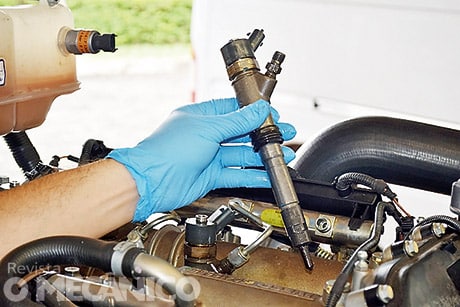
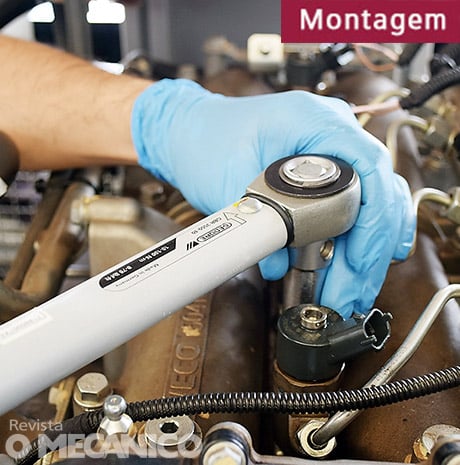
16. A bancada utilizada por Rafael Amorim para o teste definitivo e individual em cada injetor é a EPS 200, na qual o injetor passa individualmente por cinco testes: estanqueidade (onde é submetido a 1.700 bar de pressão), teste de marcha lenta, teste de plena carga, teste de pré-injeção e de emissões. “Os testes no motor são uma forma de acelerar o diagnóstico. Somente uma bancada consegue realizar um teste com precisão”, afirma o especialista da Bosch.

17. Se o injetor for reprovado no teste de bancada, Rafael revela que o componente pode ser reparado. Porém, para executar esse serviço, além de ferramental e ambiente de reparo adequado, é imperativo ter treinamento específico, já que o mecânico vai lidar com calços com precisão de milésimos de milímetro(17a). O ferramental consegue fazer a medição das folgas internas do injetor com a mesma precisão de fábrica, através de um software que indica qual é o calço específico que precisa ser instalado. Caso os valores dos calços fi quem fora do especificado, pode ocorrer danos ao motor e ao próprio injetor (17b). Após o reparo, o injetor deve ser novamente testado em bancada. Sem o ferramental ou o treinamento adequado, não tente reparar o injetor: faça a substituição do componente.
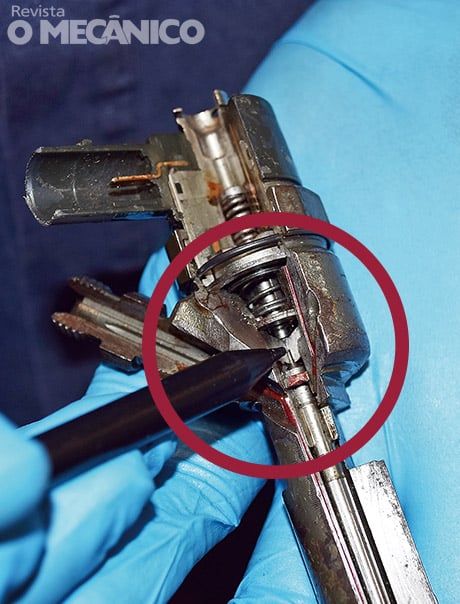

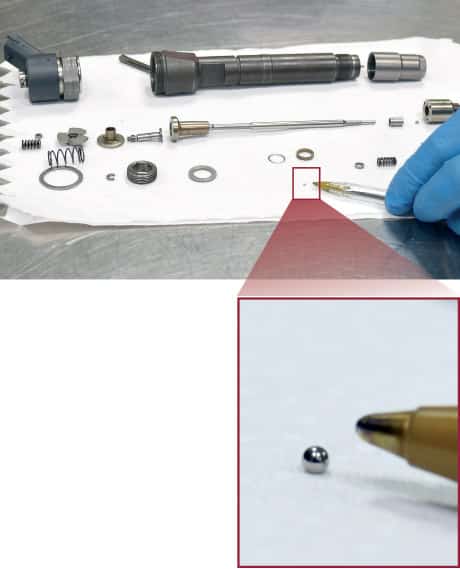
OBS: Rafael chama a atenção para a pequena esfera que é a responsável pelo acionamento do injetor. Com apenas 1,50 mm de diâmetro (esse valor varia de acordo com a família e geração do injetor), a esfera libera o fluxo de combustível para o retorno, causando o desequilíbrio hidráulico dentro do injetor que resulta na injeção de combustível no cilindro (17c).